Tig Wire Cutting Cum Embossing Machine
Meticuluos
Every Single product that we are manufacture is a result of utmost care, attention to details, precision that we put in to it.
Specification:
Model No. | ASSOMAC-SCE-TIG-1 |
Machine | Steel Fabricated Construction |
Material | S.S. Wires Copper Coated Steel Wires |
Wire Range | ∅ 1.6 to 4.0 mm |
Feeding Speed | 45 to 60 mtrs./min. |
Cutting Length | 500 mm to 914 mm / 1000 mm |
Straightening Method | Spinner type by replaceable bushes |
Cutting Method | Shear cutting hydraulic actuated |
Embossing Method | By modular embossing on both ends of TIG wire |
Optionals | Pay off for Spools or Stems |
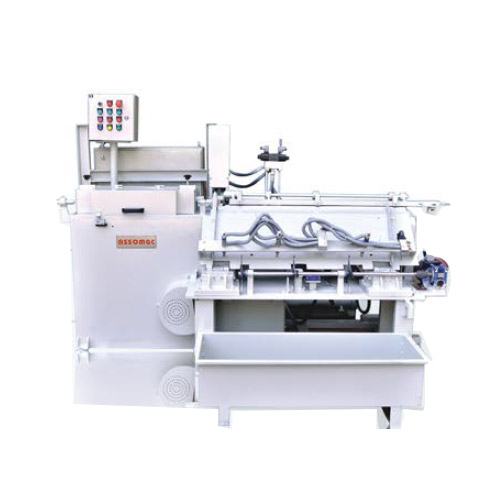
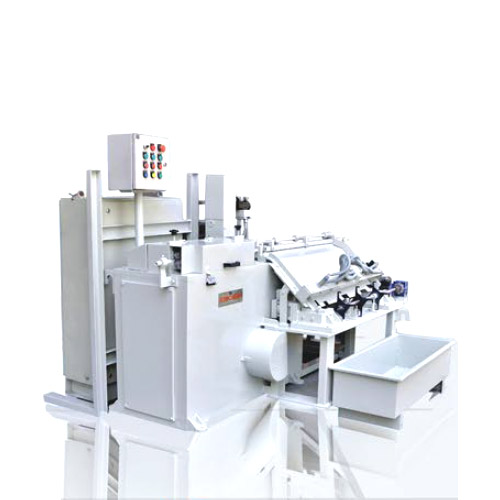
Welded Wire Mesh Machine for Meshes in Sheets or Roll Form with MS, SS or GI Wires
Assomac group has established itself as one of the leading names in the field of Wire & Wire related products. The use of Welded Wire Mesh is increasing day by day. These Wire Mesh products are now extensively used in Residential, Industrial Roads, Highways, Commercial Buildings, High-rise Tower Buildings, Dams, Tunnels & the application goes on & on.
Our Welded Wire Mesh Plants are versatile in working with line & cross wires from coils / precut the maximum welding speed is up to 90 strokes/min. Our plants are suitable for making Wire Mesh out of plain as well as ribbed wires.
Material :
Material should be of fusion quality. Low carbon & un-alloyed steel is highly recommended. However, commercial quality wires available in market can also be used up to a certain extent.
Working Procedure :
The line wires are pulled from coils, cross wires are pre-straightened and cut to length, which are then fed into the welding stations one after the other automatically.
Line wires are pulled through advance carriage with a predetermined length (distance between cross wire) and cross wire are dropped by a highly reliable system of magnets. Fusion of line wire with cross wire is done by resistance welding transformers which are controlled by micro-processor based digital welding controllers and the same is variable.
Technical Specifications of Welded Wire Mesh Machine :
AWM - 4 | AWM - 5 | AWM - 6 | |
Max. Welding Width (mm) | 1500, 2000, 2500 | 1500, 2000, 2500 | 2000, 2500, 3200 |
Line Wire Diameter (mm) | 2 - 4 | 2.5 - 5 | 2.5 - 6 |
Line Wire Spacing (mm) | 25, 40, 50, 75, 100 | 50, 100, 150 | 100, 150, 200 |
Cross Wire Diameter (mm) | 2 - 4 | 2.5 - 5 | 2.5 - 6 |
Cross Wire Pitch (mm) | 25 - 150 | 50 - 200 | 50 - 300 |
Max. Strokes / Minute | 90 | 90 | 90 |
*The above Technical Data refer to standard equipment, it can be customized to suit individual customer requirement.
Welding control panel is separate from main welding unit and is responsible for controlling the welding time and welding power.
Control panel is divided into three sections and follows principles of micro-processor control which is the most advanced and precise form of controlling weling. Our new design of control panel has in-built MCCB of 630 Amps with a fuse unit and power distribution arrangement. The new design requires less cable for power distribution.
Auxilliary Equipments :
- Pay-off : Payoff units capable of loading 2 coil of 100 kgs. each or single coil up to 250 kgs.
- Line wire straightener : multi roller straightener, width depends on machine model.
- Repair Welding Machine
- It comprises of a resistance butt welding transformer, 1 welding gun and actuator unit including a 2 phase 150 Amp contactor unit.
Key Features :
- Rigid, robust and very accurately machined body structure which gives unmatched performance and mesh of superior quality and finish.
- Highly reliable magnetic cross wire dropping system.
- All moving part suspended on roller, needle or ball bearings.
- Precise control of wire fusion.
- Higher visibility of all the welding points enables greater control.
- Ergonomically designed space for ease of operation.
- Temperature sensors are provided at every heat generation point and in occasion of overheating the machine automatically stops and prevents undue damage to machine and electrical systems.